Contents
- An overview: Digital twinning definition and its main features
- How to deploy digital twins for warehouse management?
- Benefits of digital twins for warehouse management
- Remaining challenges of Digital Twin for Warehouse management
- Outstanding case study in the manufacturing sector
- Thrive with digital twin, IoT, and more!
Digital Twin promises several advantages for Warehouse management, but what is this concept? Can it apply to your business?
Digital Twin, a concept that originated in the space industry, is gaining attention due to its vast potential in various sectors, including Logistics. This series of articles will go through Digital Twin’s application in several aspects of Logistics, starting from Digital Twin for Warehouse Management.
An overview: Digital twinning definition and its main features
Definition
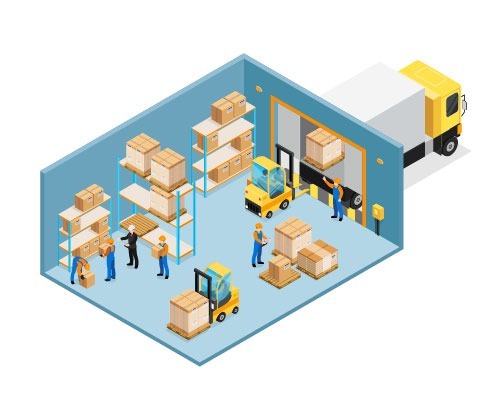
DHL defines a digital twin as “A unique, virtual model of a physical thing.” It typically connects to the thing and updates itself in response to known changes to the thing’s state, condition, or context. “
The origin of the concept dates back to 2002 when Dr. Grieves from the University of Michigan gave a presentation called “Conceptual Ideal for Product Lifecycle Management.”
The concept in this paper contains all the key elements of Digital Twins, which are:
- a real entity,
- a virtual entity,
- data flow from the real entity to the virtual entity and vice versa
- virtual sub-entities.
Afterward, NASA adopted and developed the theory. Using paired simulations, it refined and selected the optimal solutions for the Apollo 13 spacecraft repair in 1970. The technique continued to evolve and became digital twinning in the early 2000s but only gained popularity when key supporting technologies reached a certain maturity. Some of those are:
- low-cost data storage and computing power
- fast wired and wireless networks
- affordable and proper sensors
The main goal of a digital twin is to create, build, and test equipment in a virtual environment before applying changes to the real entity. In that sense, creating a digital twin not only helps cut prototyping or construction costs but also predicts failures. Hence, it can reduce both maintenance costs and downtime.
A digital twin comprises several elements:
- manufacturing simulations
- 3D CAD models
- real-time data from sensors that are incorporated into the physical operating environment.
Main features
DHL also indicates that digital twinning is much more complex than other pre-existing 3D modeling methods, and there are numerous contributors to this advanced simulation model. However, the majority of experts agree on five key factors below that distinguish digital twining:
- Sensors and actuators from the physical world
- Integration
- Data
- Analytics
- Continuously updated digital twin application
How to deploy digital twins for warehouse management?
According to SAP, the implementation of a digital twin depends on the intended business outcome and the sophistication of business logic. For most connected products and assets scenarios, there are four scenarios for digital twin implementation as follows:
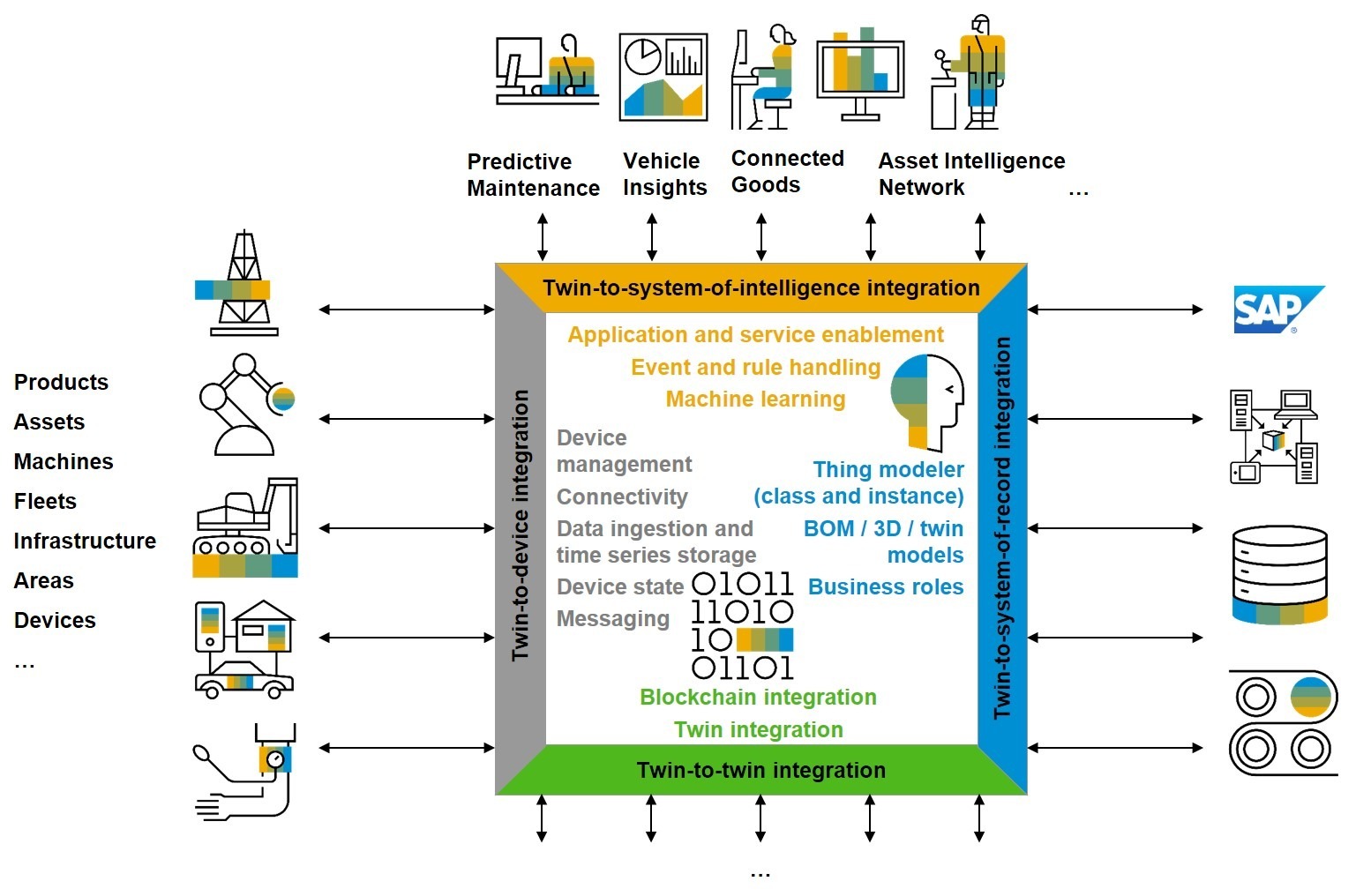
- Twin-to-device integration: The real entity needs to be securely connected and managed. Streams or batches of live data require protocol conversion, semantic mapping, and transformation before being ingestible into a big data store infrastructure. This allows querying object state and history information captured as a time series.
- Twin-to-twin integration: If the physical object is not managed by the provider of the digital twin, an optional twin managed by a service provider or a supplier may be needed.
- Twin-to-system-of-record-integration: Integration with business information and engineering systems provides essential context along the lifecycle of the physical object:
- PLM for engineering bill of material, components and spare parts, software versioning (for embedded systems)
- CAD/CAM/CAE for 2D and 3D models, layouts, assembly information
- Manufacturing systems for product traceability, serialization, and manufacturing bill of material
- ERP for product variants and financial information, equipment, and spare parts inventory
- ERP/CRM and supplier networks for service contracts, business partners and rolls, SLAs
- Twin-to-system-of-intelligence integration: Most digital twins interact with systems of intelligence through events and notifications while exposing condition monitoring and historical information; rule handling, data science algorithms, and machine learning create insights from live data streams and provide predictions on future states.
Implementing the digital twins will largely be managed from the cloud to facilitate the above network-centric engagement model. However, not all the relevant data is transmitted. In many cases, only events and change information will be sent into the cloud as a stream, while data locally and temporally persisted can be replicated to resolve underlying issues and to evolve algorithms.
Read more: Digital Twin Series Part 2: Digital Twin Application in Shipments
Benefits of digital twins for warehouse management
According to McKinsey, the global budget spending on warehousing is around $350 billion, and it keeps increasing each year. With digital twin applications, warehouse efficiency is predicted to rise by 20–25%. This improvement will likely bring about notable operating and capital expense savings.
Digital twinning allows companies to gain a bigger picture of warehouse operations and make drastic changes rather than settling for partial enhancements of the current layout and process.
This technology enables better estimation of potential effects of mechanization and automation possibilities, covering all the spectrum of vendors and products available.
Firms can resort to digital twins in VR/AR personal training. For instance, DHL deploys AR/VR picking systems training with wearable equipment gadgets such as Google Glass Enterprise Edition or Microsoft HoloLens to help employees practice vision picking tasks on simulations before delivering the job.
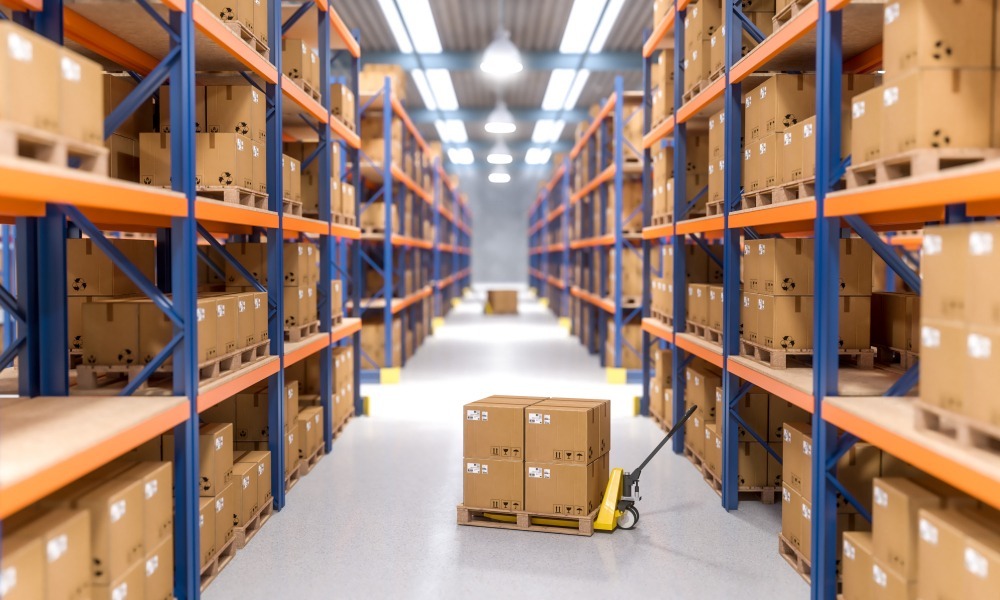
The following section discusses the major benefits of building a digital twin.
All-around-the-clock operation
First of all, warehouses generally operate 24/7, and it is very costly to shut them down for rearrangement and optimization. However, it would be detrimental if companies weren’t to seek renovations. The complexity of stock-keeping units (SKUs) classification (due to the rapid expansion of e-commerce) is increasing, and the competition for providing faster delivery is on the rise.
McKinsey indicates that Digital Twinning can generate virtual avatars of every asset in the warehouse and conduct simulations on floor plans, workflows, SKU mix, and shipment profiles. This approach could be more cost-effective than shutting the warehouse to run tests in the long term.
Various factors in the warehouse can impact assets’ conditions
Secondly, various factors in the warehouse can impact the assets’ conditions. Given that Digital Twin represents an entity at one specific condition, companies can examine different possibilities of an item in other situations without the risk of damaging it.
Improve Quality control procedures
Thirdly, current quality control procedures require a large amount of manual work. Meanwhile, Digital Twin can update the host object’s status continuously. We can also save more human capital if assets’ conditions are supervised automatically and only need manual checks in specific cases.
Solve difficulties in micro and macro governance
Finally, warehouse complexity creates difficulties in micro and macro governance. Thus, the ability to simulate different parts and functions of the warehouse both mutually and individually would facilitate experts to see issues both holistically and in detail.
Suppose digital twinning is correctly integrated with other advanced techs such as intelligence (AI), machine learning, and augmented/virtual reality (AR/VR). In that case, managers can gain insights and teach the system to solve similar problems next time they arise.
Remaining challenges of Digital Twin for Warehouse management
Despite promising advantages, manufacturers still face difficulties developing and integrating digital twins into Warehouse Management’s current operation. DHL analyses seven main obstacles that are worth considering:
- Cost: considerable initial investment in platforms, model development, and maintenance.
- Precise representation: impossible perfect simulation leads to unavoidable assumptions, simplifications in model development, and compromise with the desired outcome.
- Data quality: underlying risks from inconsistencies of data streams
- Interoperability: limited alternatives of technology providers.
- Education: Adoption of new working processes that challenge change management and ability building.
- IP protection: risks of product and customer data exposal that require more restricted data ownership, identity protection, data control, and access governance.
- Cyber Security: possible new points of entry for cybercriminals.
Confronting these obstacles requires lots of effort from the business. However, Mrs. Janina Kugel, board member and Chief HR Officer of Siemens, suggests that the change must be rooted in a leadership approach. Managers and leaders should be more open to learning, guiding, and empowering their employees toward the new technology shift that was merely fictional 20 years ago. Managers and leaders must enhance their knowledge, communication, and other soft skills.
In a nutshell, Digital Twinning is a promising technology with multiple applications that could benefit warehouse management. It is predicted to be one of the change-makers in the sector soon. Thus, it is wise to research and consider appropriate adoptions for your warehouse to keep pace with or even gain a competitive advantage in the logistics industry.
Outstanding case study in the manufacturing sector
From the idea of a visionary South Korean start-up company, GEM developed a dynamic virtual marketplace for the manufacturing sector. The enablement of rapid and transparent supplier-buyer communications is the online platform’s most striking advantage. The case study also stands out due to the amount of technical consultancy input provided by GEM.
Thrive with digital twin, IoT, and more!
Manufacturing and logistics are dynamic and rapidly changing sectors with new challenges to overcome and also various opportunities to boost business success.
With proven expertise in digital solutions and award-winning development services, GEM Corporation is trusted by leading clients in the field to help them reap the full benefits of cutting-edge technologies including IoT, AI, and so many more.
Drop your information in the form below and let’s get started.
Error: Contact form not found.