Contents
Manufacturers are under growing pressure to streamline operations, manage supply chain volatility, and improve production planning, all while keeping costs under control. ERP solutions for manufacturing have become a strategic tool to meet these demands, helping companies unify data, standardize processes, and gain better visibility across their operations. The global ERP market is projected to reach $96 billion by 2032, reflecting sustained investment across industries. This article outlines how ERP can reshape manufacturing, from core capabilities to practical steps for implementation.
What are ERP Solutions for Manufacturing?
ERP solutions for manufacturing are integrated systems designed to coordinate and manage core business processes across production, planning, inventory, procurement, finance, and quality control. They serve as the operational backbone for manufacturing firms, helping stakeholders make informed decisions based on real-time data and standardized workflows.
Traditional ERP vs Modern ERP
Traditional ERP systems were often built as monolithic platforms – on-premise, complex to customize, and rigid in their deployment. While effective at consolidating data, these systems came with high upfront costs and long implementation cycles. Their architecture made it difficult to adapt quickly to changing business needs or scale across global operations.
In contrast, modern ERP solutions tailored for manufacturing are modular, cloud-based, and more flexible in design. These platforms support dynamic production environments by offering real-time data access, seamless updates, and easier third-party integrations. Modular structures also let manufacturers adopt functionality incrementally, rather than committing to a full-suite rollout. This shift enables faster deployment, lower maintenance costs, and a closer fit with evolving operational models.
Popular Manufacturing ERP Solutions
Several ERP platforms have gained traction in the manufacturing space:
- NetSuite: A cloud-native ERP system that supports multi-plant operations, supply chain planning, and real-time inventory visibility. Its flexibility makes it well-suited for mid-sized manufacturers with growth ambitions.
- SAP S/4HANA: A real-time enterprise suite that supports advanced manufacturing scenarios, including predictive analytics, digital twin modeling, and integration with industrial IoT systems. It is widely adopted by large manufacturers with complex global operations.
- Microsoft Dynamics 365: Offers a modular approach to ERP and CRM, with specific capabilities for discrete and process manufacturing. The platform integrates easily with Microsoft’s broader ecosystem, making it attractive for organizations already using Microsoft tools.
Benefits a Manufacturing ERP System Offers
A manufacturing ERP system delivers a measurable impact when aligned with operational goals. Organizations often adopt ERP platforms to replace fragmented legacy systems and move toward real-time, integrated decision-making. According to survey data, 83% of companies that conducted ROI analysis before implementation reported meeting their expectations after one year.
Below are the key benefits, structured around core manufacturing priorities:
Operational Visibility
- Unified dashboards give real-time access to production data, order statuses, and inventory levels.
- Decision-makers can spot bottlenecks or anomalies early, reducing unplanned downtime.
- Centralized reporting improves collaboration across departments and geographies.
Production Planning Accuracy
- ERP systems automate scheduling based on capacity, materials availability, and demand forecasts.
- Manufacturers can balance workloads across multiple lines or facilities, minimizing delays.
- Data-driven planning reduces reliance on manual spreadsheets and disconnected tools.
Inventory Control
- Real-time inventory tracking helps avoid both overstocking and stockouts.
- Automation in procurement and replenishment keeps inventory levels aligned with actual demand.
According to recent surveys, 62% of companies noted cost savings in purchasing and inventory after ERP adoption.
Compliance Tracking
- ERP platforms maintain audit trails for quality checks, supplier certifications, and regulatory reporting.
- Built-in compliance features help manufacturers adhere to industry standards without added manual effort.
- Traceability features improve recall management and customer assurance.
Centralized Data Management
- A single source of truth reduces errors from duplicate or inconsistent data sets.
- Cross-functional teams – from finance to operations – work off the same data, improving coordination.
- Consolidating systems simplifies IT management and reduces maintenance costs.
Supply Chain Optimization
- ERP systems offer visibility into supplier performance, lead times, and logistics tracking.
- Integrated procurement and vendor management support more resilient sourcing strategies.
- Predictive tools help anticipate disruptions and adjust plans accordingly.
Customer Relationship Management (CRM)
- Built-in CRM modules capture sales orders, customer interactions, and service requests.
- Sales and production teams can coordinate delivery timelines based on real availability.
- Consistent service levels improve retention and customer satisfaction.
As ERP systems grow more modular and cloud-based, manufacturers continue to invest. Half of companies are acquiring, upgrading, or planning to update ERP systems to modernize operations and consolidate disparate tools. The long-term value lies in the system’s ability to align with how the business operates, while keeping data, processes, and teams in sync.
Core Features of ERP Solution for Manufacturing
A manufacturing ERP system brings together operational, financial, and supply chain processes under one framework. Its core features are designed to support cross-department collaboration, improve resource planning, and strengthen decision-making.
Manufacturing Execution System (MES) Integration
- Connects ERP with shop floor systems to synchronize planning with production.
- Real-time data from machines, sensors, and operators flow into the ERP, enabling dynamic adjustments to schedules and resource allocation.
- Supports quality control, downtime tracking, and work order management at the execution level.
- Helps operations and IT teams align on metrics such as throughput, yield, and utilization.
Demand Forecasting
- Uses historical sales data, seasonal trends, and external signals to project product demand.
- Supports procurement and production planning teams with more accurate material requirements and inventory targets.
- Helps finance and sales departments align revenue projections with operational capacity.
- Reduces risk of stockouts or excess inventory, improving working capital efficiency.
Bill of Materials (BOM) Management
- Centralizes product structure data, including components, subassemblies, and raw materials.
- Links design, procurement, and manufacturing teams by maintaining version control and change histories.
- Supports make-to-order and engineer-to-order workflows with dynamic BOM customization.
- Ensures procurement and production stay aligned with engineering specifications.
Real-Time Reporting and Analytics
- Offers live dashboards and automated reporting for KPIs across operations, finance, procurement, and logistics.
- Helps executives and plant managers monitor performance with up-to-date data, without waiting for end-of-month reports.
- Enables scenario modeling and cost analysis for better budgeting and resource planning.
- Reduces reliance on manual reporting processes and disconnected spreadsheets.
How to Transform Your Factory with a Manufacturing ERP System?
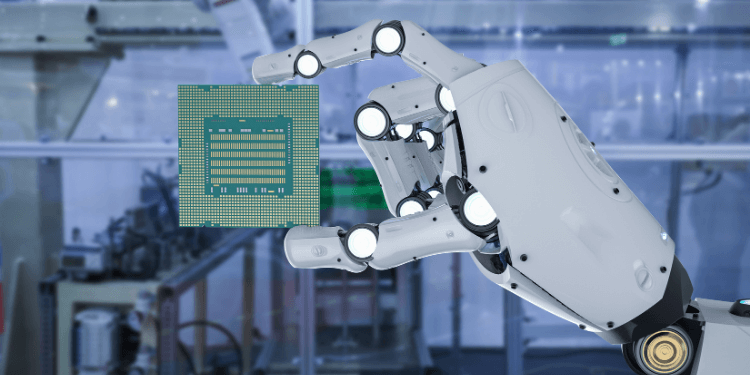
Transforming a factory with a manufacturing ERP system is a staged process that touches every part of the business. When planned and executed with clear alignment between technology and business objectives, ERP becomes a structural foundation for operational control, cross-functional coordination, and data-driven decision-making.
1. Leadership Alignment and Strategic Priorities
The first step lies in securing leadership alignment. ERP systems touch nearly every function, from procurement and production to finance and sales, which means leadership must define what success looks like. Whether the goals are shorter production cycles, real-time inventory visibility, or improved cost control, executive teams need to set clear priorities and reinforce them throughout the implementation process. These priorities should translate into measurable outcomes, such as improved order fulfillment rates or faster month-end closing.
2. Cross-Functional Planning and Collaboration
Cross-functional collaboration is equally important. ERP systems are built on standardized workflows and shared data models, which means departments must move away from siloed processes. Involving operations, finance, procurement, and IT early in the planning phase helps surface process gaps and avoids misalignment during rollout. These teams should co-design workflows and reporting structures that reflect actual business needs—not just system defaults.
3. Data Migration and Governance
One of the most overlooked aspects of ERP transformation is data migration. Legacy systems often contain inconsistent, redundant, or outdated information. Cleaning and structuring this data before it moves into the new system is critical. Without a clean foundation, even the most advanced ERP tools can produce unreliable outputs. Establishing clear rules for data ownership, access, and updates also strengthens long-term governance and decision-making.
4. Phased Rollout and Operational Testing
A phased rollout model offers practical advantages. Rather than switching over all functions or plants simultaneously, companies often choose to implement ERP modules in stages. This approach reduces operational risk, gives teams time to adapt, and allows for iterative improvements. Early pilot phases can uncover configuration issues or user challenges before broader deployment.
5. Change Management and Workforce Readiness
Finally, no ERP transformation succeeds without thoughtful change management. Systems introduce new interfaces, reporting tools, and approval workflows that can disrupt established routines. Preparing teams for these shifts requires training manuals as well as ongoing communication, role-based training, and support structures to guide users through the transition. When employees understand not just how the system works, but why it matters to the business, adoption becomes smoother.
GEM Corporation is a global technology consultancy specializing in end-to-end digital solutions for enterprises across Australia, Japan, Korea, and U.S., EU. Since 2014, we’ve delivered more than 300 projects across diverse industries, combining deep domain knowledge with a robust engineering practice. Our services span software development, cloud engineering, data platforms, and enterprise systems to align technology with business strategy.
We’ve worked extensively with manufacturing clients to build and optimize ERP systems that support real-time operations, integrated supply chains, and scalable production models. Our team brings practical experience in connecting ERP platforms with MES systems, designing modular architectures, and improving data visibility across plants and geographies. Whether it’s modernizing legacy ERP or implementing a cloud-native solution, we help manufacturers align their systems with production goals and financial controls. With a multidisciplinary team of over 400 engineers and consultants, GEM delivers ERP solutions that are both technically sound and operationally grounded.
Conclusion
ERP solutions for manufacturing bring structure, visibility, and coordination to complex operations. When aligned with business goals, these systems support informed planning, tighter inventory control, and integrated workflows across departments. Success depends on leadership commitment, clean data, phased rollout, and collaboration across functions. For manufacturers seeking to replace fragmented systems with a unified platform, ERP offers a path toward more agile and accountable operations, positioning the factory to compete on both cost and responsiveness.
To explore how GEM can support your ERP transformation with industry-specific expertise and tailored execution, get in touch with our team.